FLOWBOX in LASSELSBERGER Production Plants
LASSELSBERGER implemented FLOWBOX to unify energy management across five production plants, achieving automated reporting, energy cost savings, and improved operational efficiency.
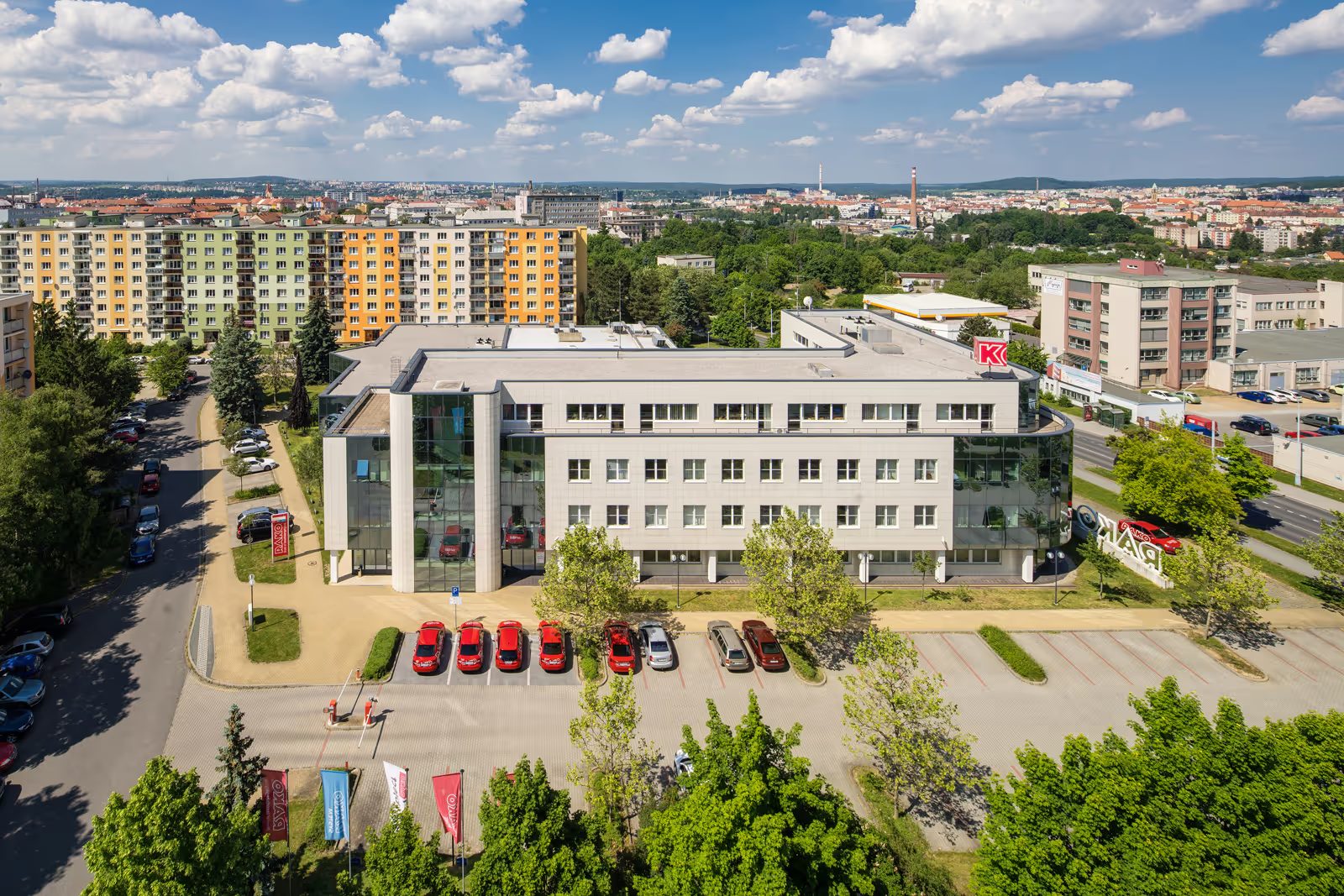
About the Company
LASSELSBERGER is a leading manufacturer of ceramic wall and floor tiles in the Czech Republic and a key player in the European market. Operating under the traditional brand RAKO, which boasts a history of more than 140 years, the company runs five production plants (RAKO 3, Chlumčany, Horní Bříza, Podbořany, and Borovany). It is committed to environmentally responsible manufacturing, as demonstrated by its EU Ecolabel certification. LASSELSBERGER is part of the Austrian LASSELSBERGER Group and exports its products to dozens of countries worldwide.
Key Numbers
- 1500 employees
- 5 production plants
- approx. 70 GWh (electricity + natural gas) per month
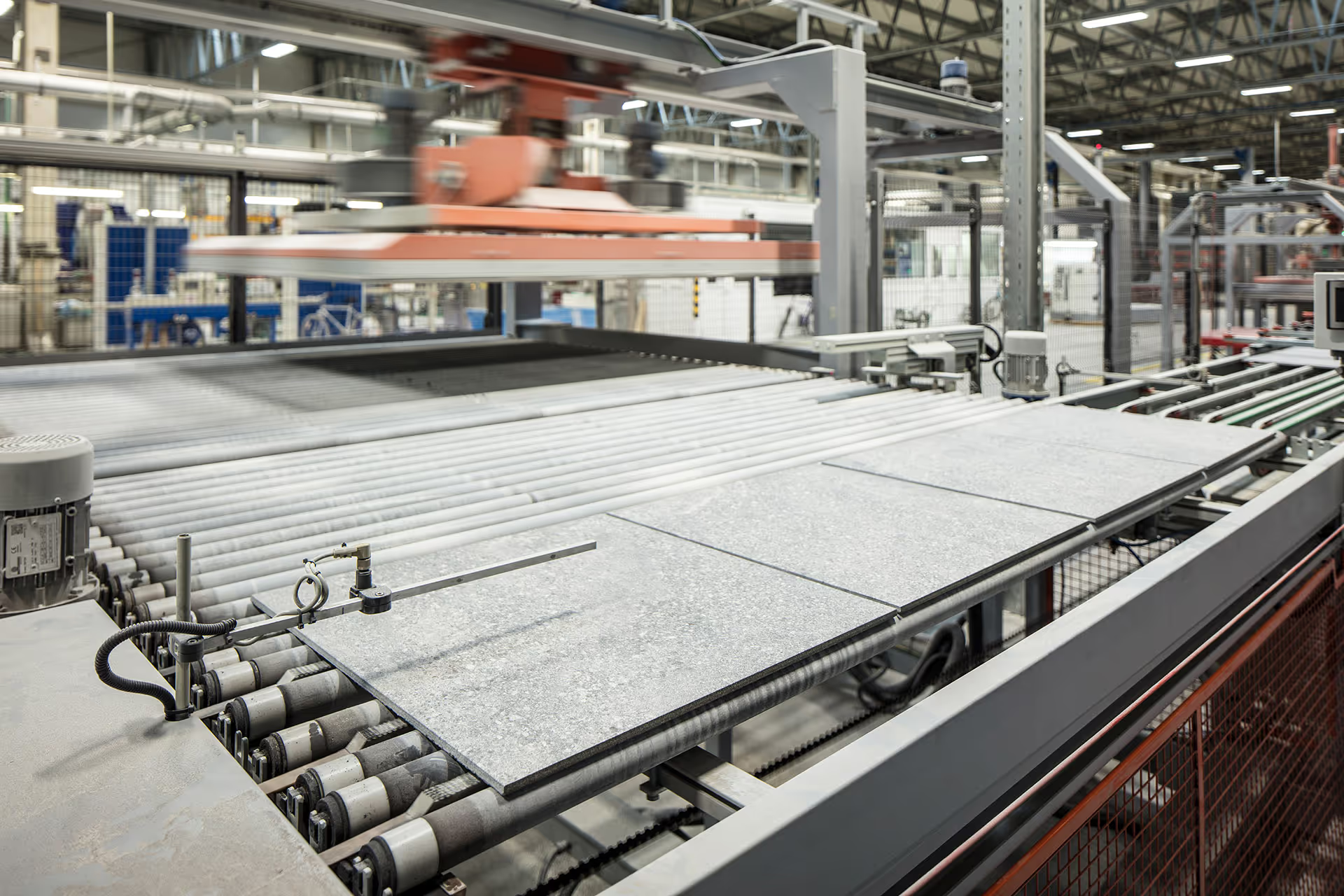
Project Objectives
The goal of the project was to implement a unified energy management system across all LASSELSBERGER production plants, automate energy consumption data collection, optimize energy usage, and ultimately reduce operating costs.
Key Benefits
- Energy cost savings - elimination of penalties for exceeding technical limits and reactive power consumption
- Automated reporting and time savings
- Improved visibility of consumption and savings across all plants
- Strategic support for decision-making
-
FLOWBOX EMOS in Action at LASSELSBERGER
Energy Dispatching
FLOWBOX collects and visualizes real-time data from sub-meters (electricity, gas, water, and air) across all production plants.
Automatic Data Submission to the Grid Operator
FLOWBOX enables fully automated reporting of energy data, eliminating manual input and ensuring compliance with regulatory requirements set by the Grid Operator.
Control of Technical Maximum
Using predictive algorithms, the system regulates energy consumption to prevent exceeding reserved capacity limits and avoid related penalties.
Evaluation of Specific Energy Consumption
The system closely monitors the energy intensity of individual technologies and production lines, providing analysis to support efficiency improvements.
Monitoring of Compressed Air and Water Consumption
Detailed monitoring of compressed air usage as well as potable, utility, and treated water consumption.
Monitoring of Indoor Temperatures in Production Halls
Environmental control within facilities to ensure optimal production conditions and employee comfort.
Unified System Across Plants and Benchmarking
FLOWBOX connects individual production plants with the central office, enabling efficiency comparisons and performance benchmarking across sites.
Measurement Across All Levels of the Energy Network
FLOWBOX collects data from all voltage levels, as well as from both medium- and low-pressure branches of the gas network.
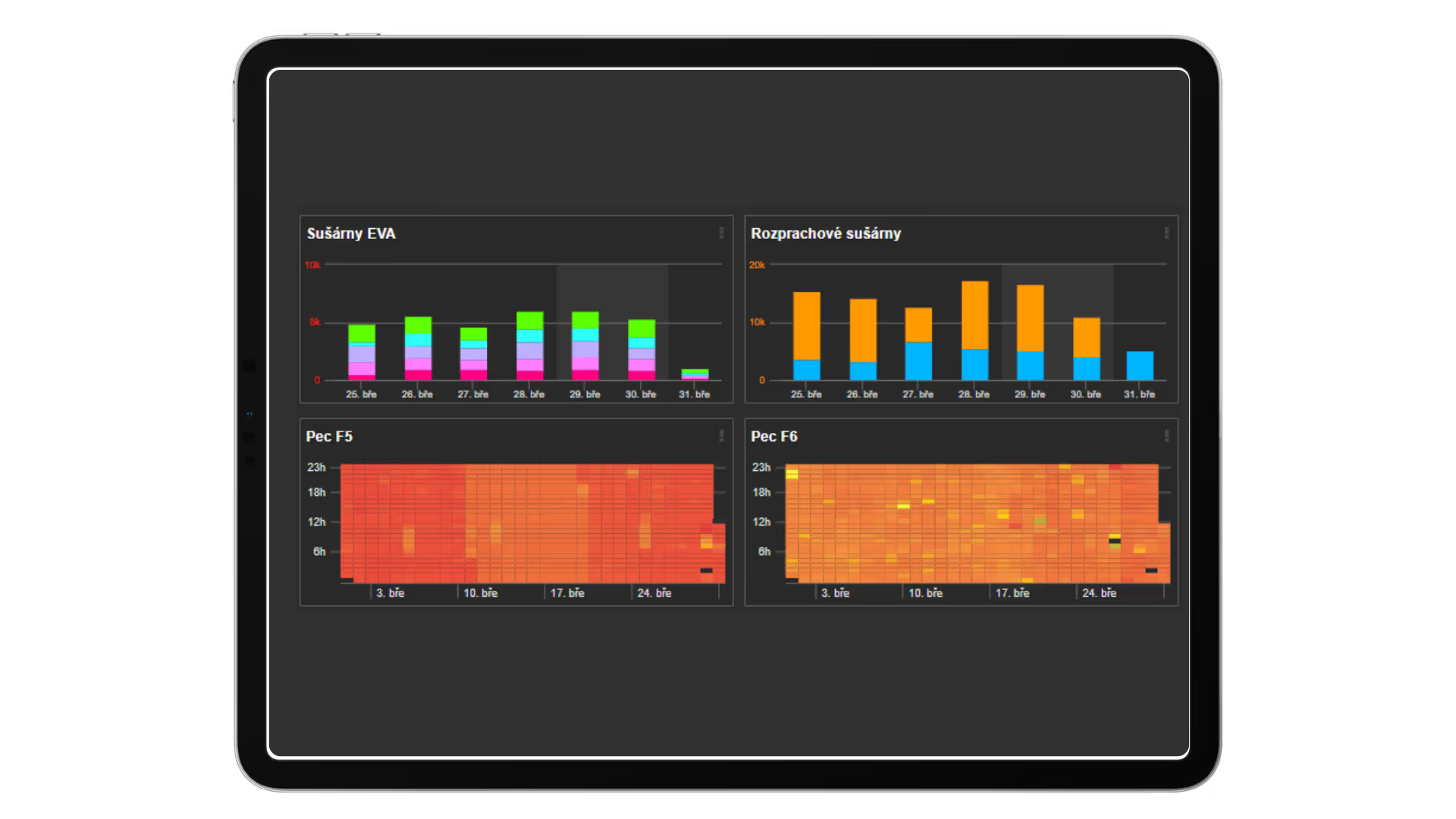
LASSELSBERGER’s Experience with FLOWBOX
“We chose FLOWBOX through a tender process, as it met all our requirements and also offered the most cost-effective solution. At our company, FLOWBOX handles energy dispatching—from collecting data from sub-meters (electricity, natural gas, water, compressed air, temperatures), to managing 15-minute electricity peaks, power factor compensation, and evaluating specific consumption in our kilns. One of the major benefits is certainly the automatic submission of data from our local distribution network to the Grid Operator.”
Tomáš Bezděk, Energy Manager, LASSELSBERGER