BAUMRUK & BAUMRUK
Discover how FLOWBOX transforms factory operations through digitalization, revealing inefficiencies and driving operational excellence. Our comprehensive measurements and diagnostics provide valuable insights into resource utilization, enabling enhanced operations control and significantly reducing wastage. By optimizing lighting, heating, and air handling, our client achieved remarkable energy savings of 37% annually, leveraging cost-effective resources and boosting production capacity without increasing workforce size.
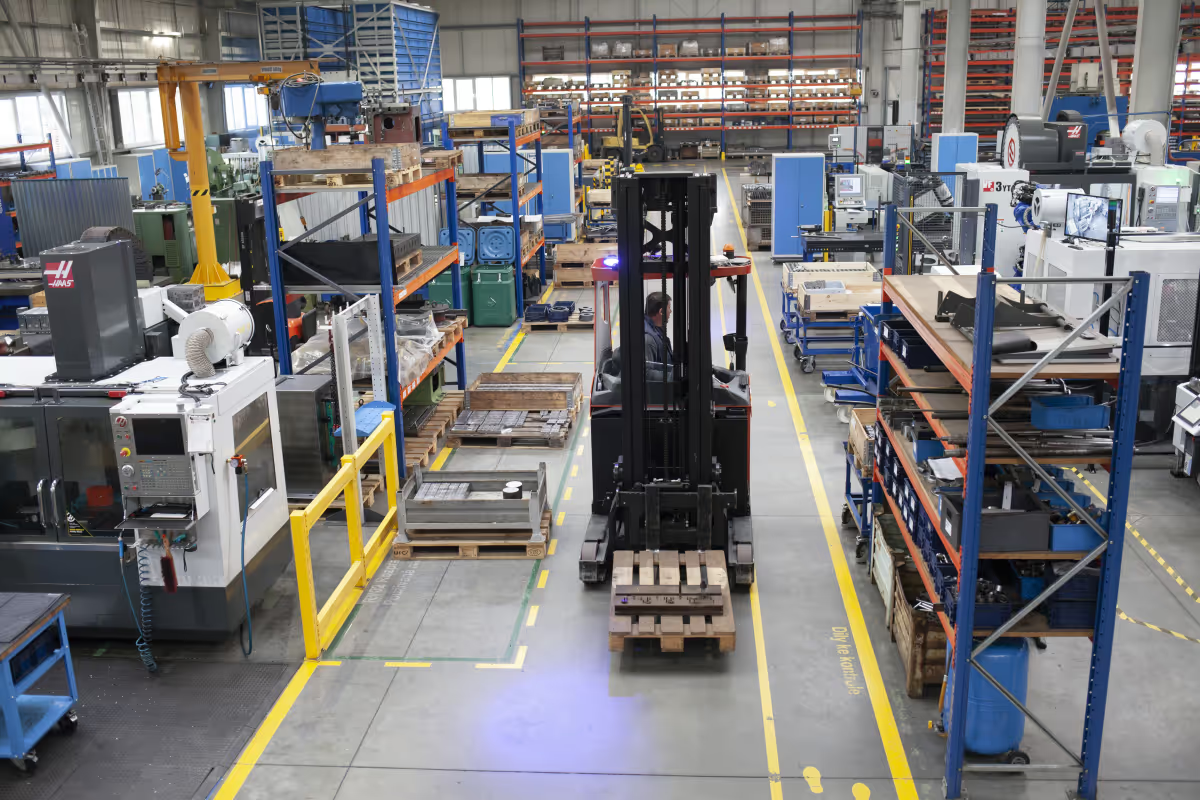
Factory production plant digitalization
The FLOWBOX Factory Manager MAN5000 digitalization product package was deployed. The measurements revealed the causes of wastage. This further provided inputs for enhanced operations control. Machine diagnostics have made it possible to increase production effectiveness. The costs of lighting, heating, and air handling have been reduced and the cheapest available resources began to be used. The company thus increased its production capacity with the same number of employees. Energy management brought an annual savings of 37 percent.
About client
The company is engaged in mechanical engineering consisting mainly of machining, laser cutting and welding of high-quality components for transport and industry for large customers from abroad. Five associated halls. In addition to electricity for production, they also consume natural gas, water and nitrogen.
INITIAL STATE
Wastage, missing inputs for operations management, ineffective production, high energy costs and unused production capacity.
DESIRED STATE
Controlled operation, effective production, optimized costs for energy resources and increased production capacity.
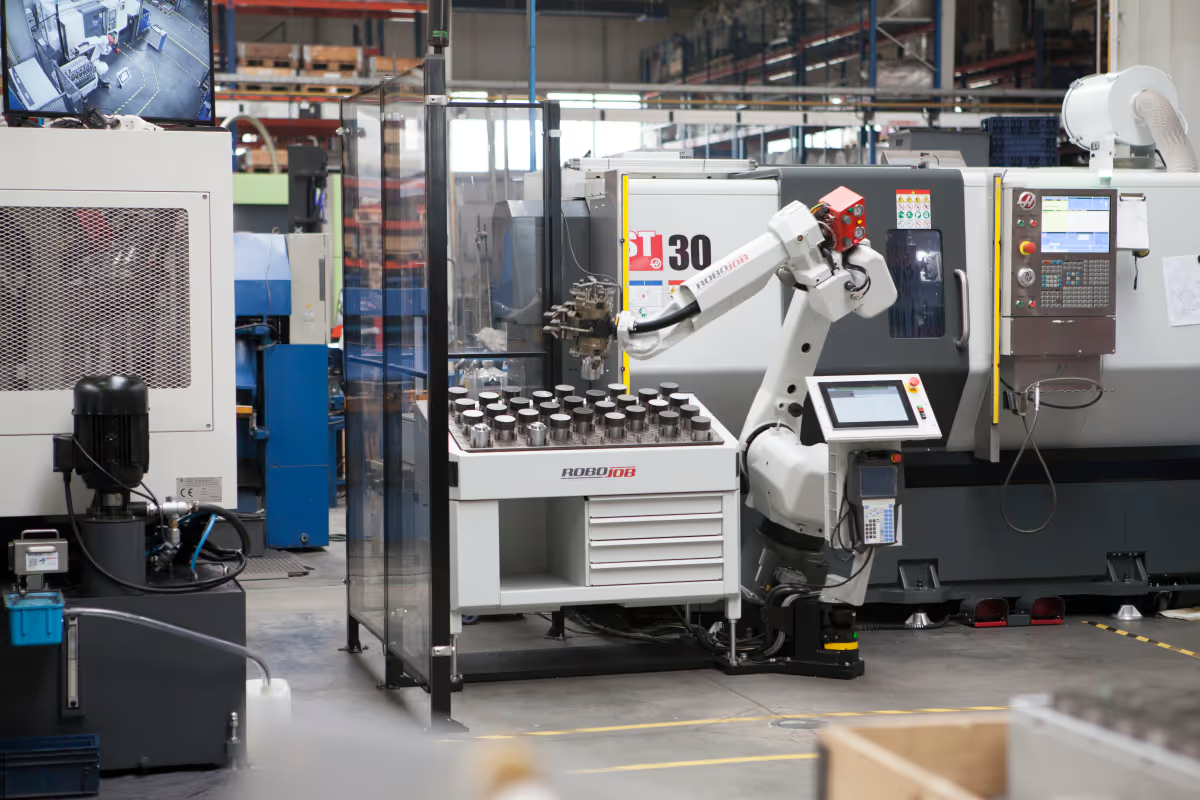
The measurements revealed causes of wastage
Continuous accurate measurements of individual operations and appliances have revealed all ineffective uses of resources and wastage. The problem was that the equipment was incorrectly set by the manufacturer, malfunctioning autonomous regulators and unwanted concurrences of air conditioners with heating.
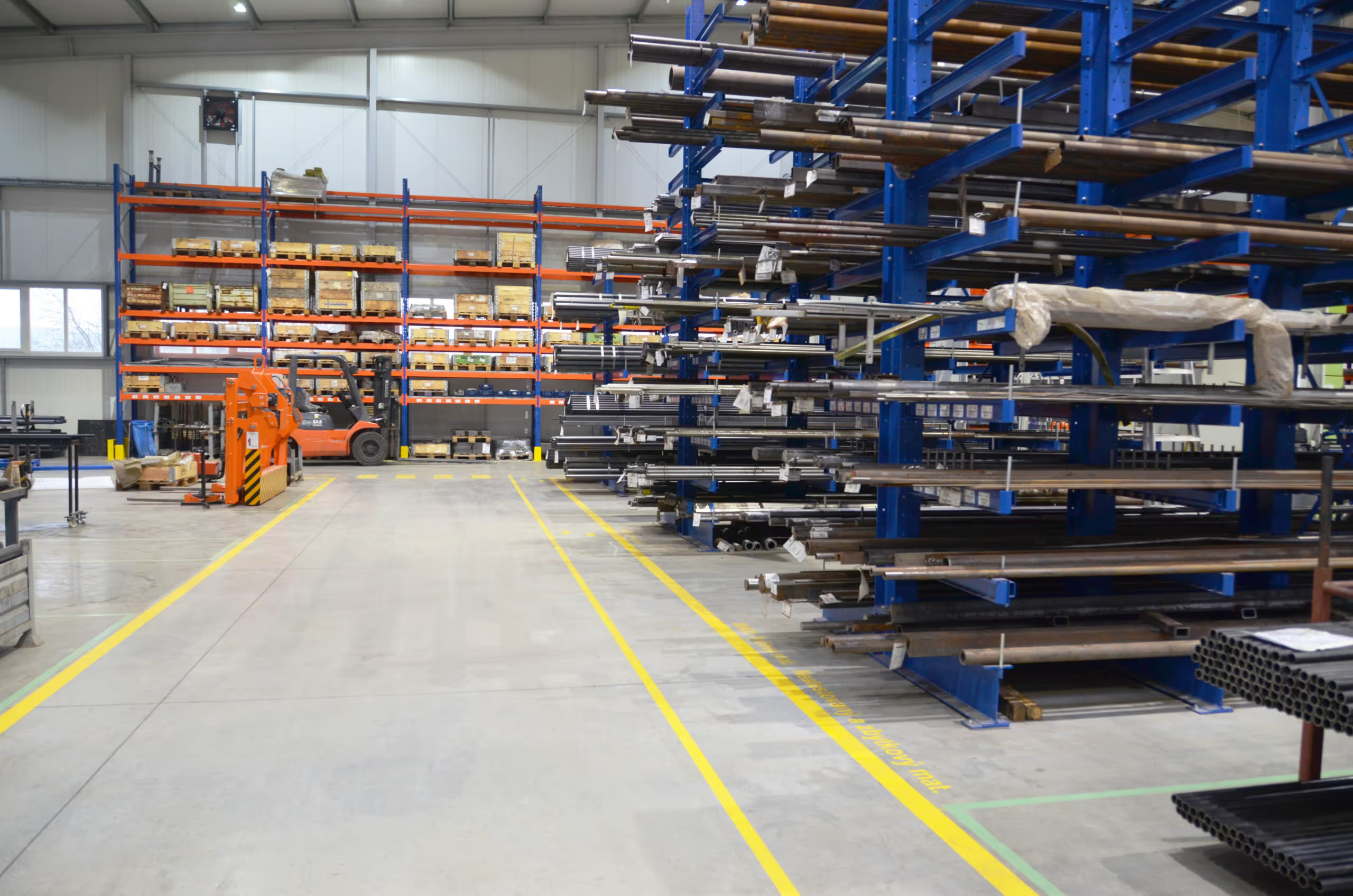
The measurements provided inputs for control of operations
Selective measurements provide accurate inputs to cost models for pricing and business management.
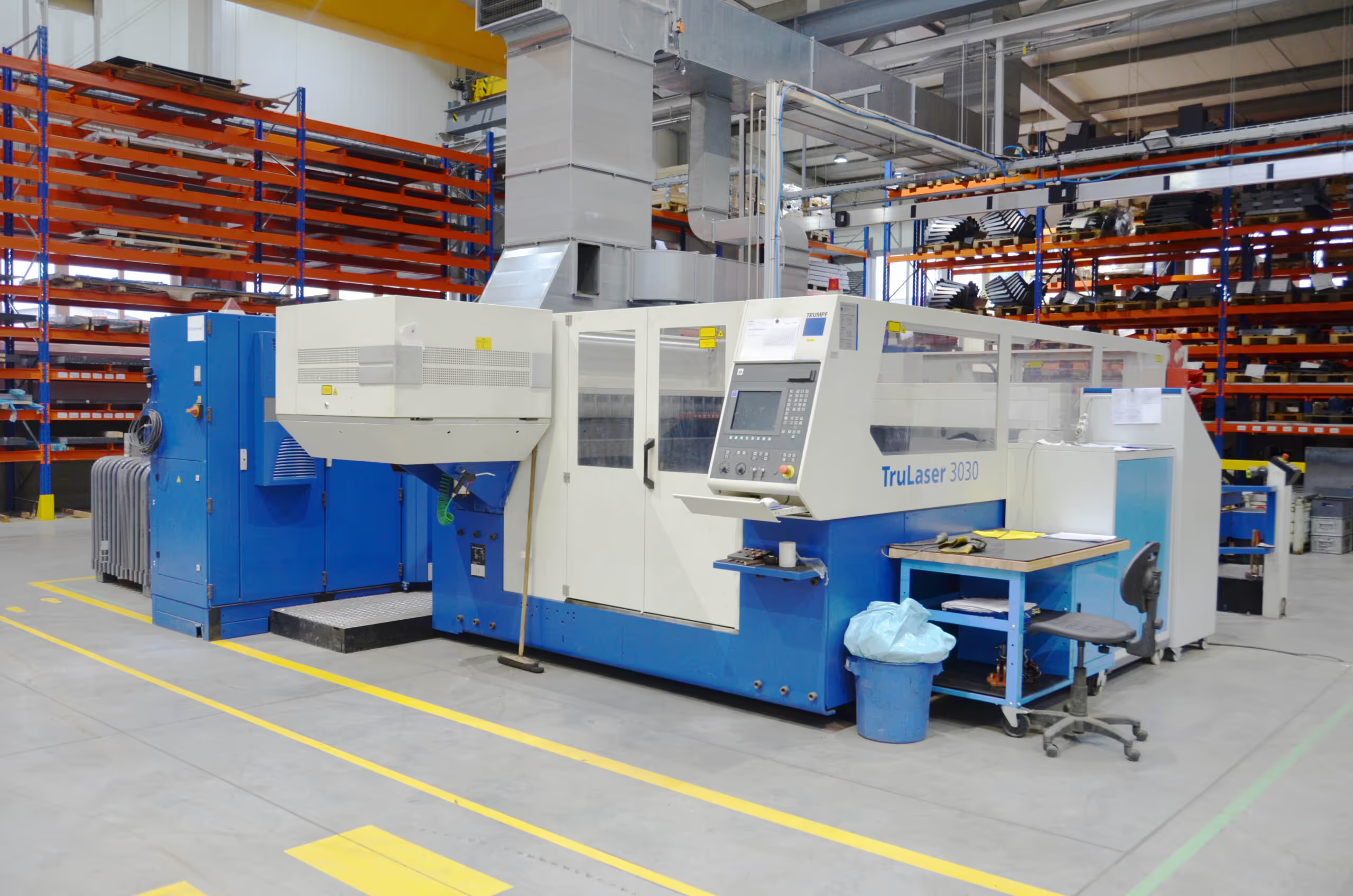
Machine diagnostics increased production effectiveness
Diagnostics of use and utilization of production technologies helped to optimize production processes. Any anomaly states in the running of production and non-production technologies are reported in a timely manner.
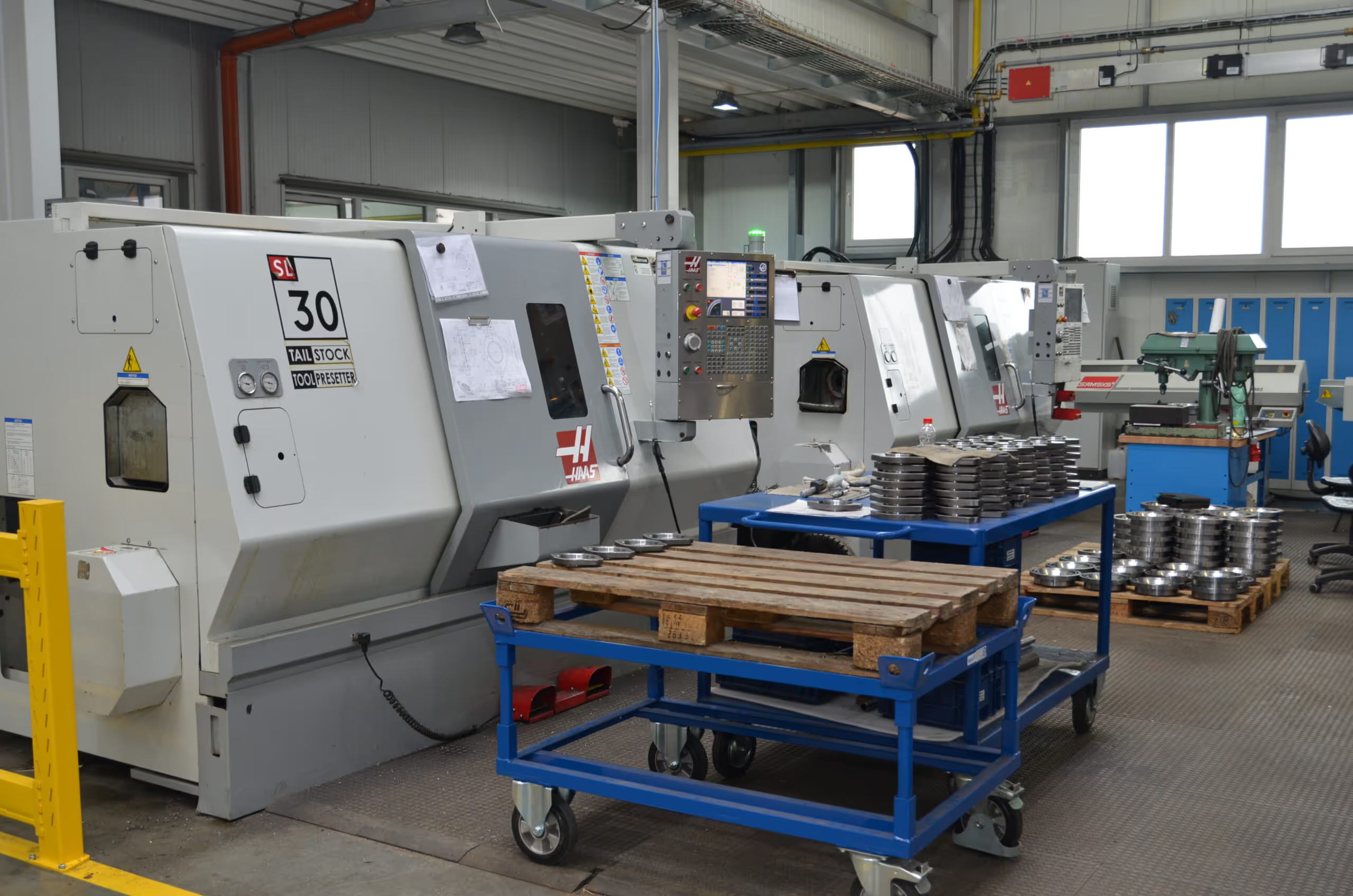
Unintentional modifications were prevented
By eliminating the intervention of unauthorized persons in the regulations of individual appliances, unintentional adjustments to the optimal settings, and thus uncontrollable and unprovable wastage, were avoided.
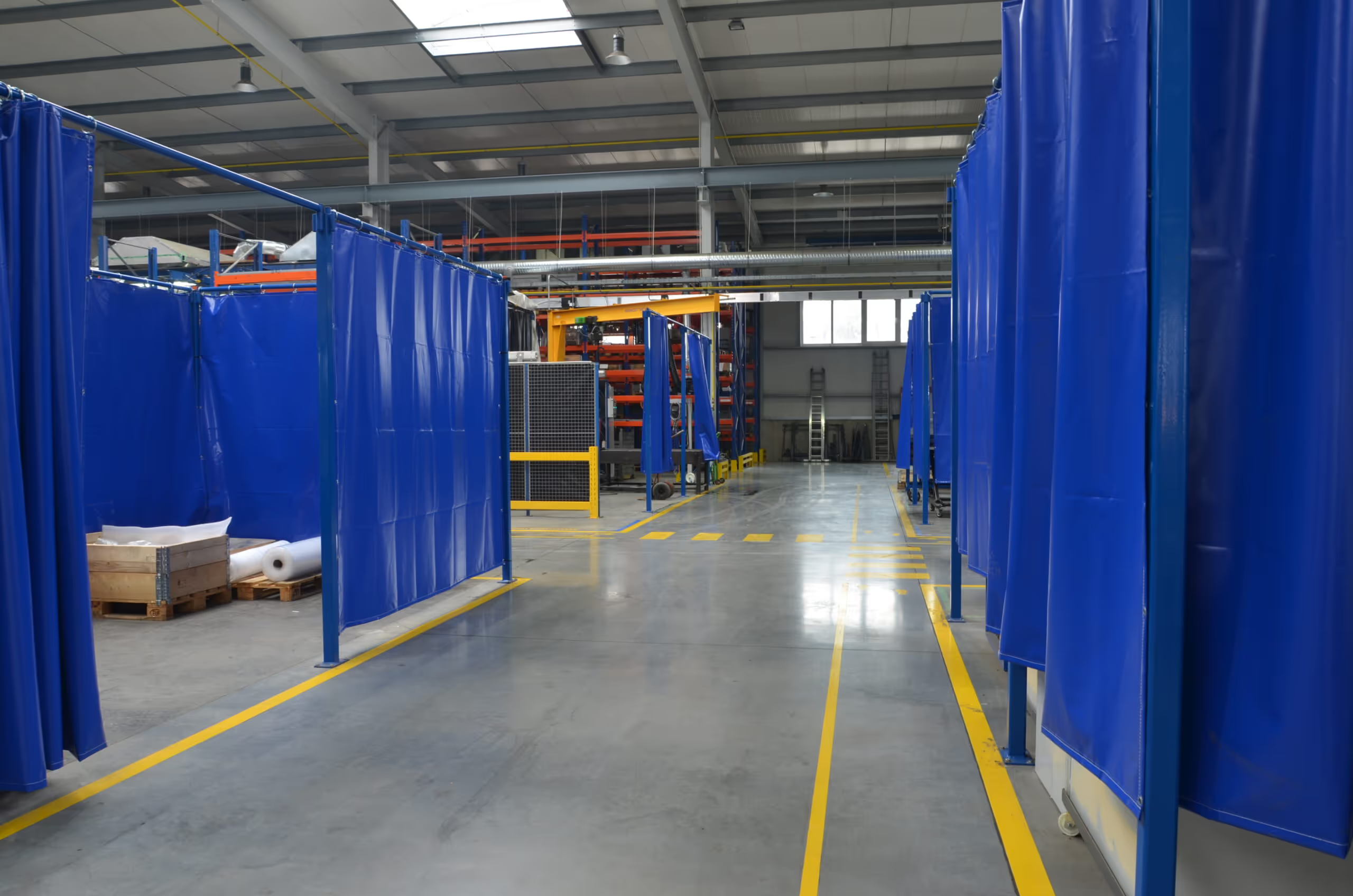
Lighting, heating and air handling have been optimized
The introduction of autonomous centralized control of HVAC systems, with the possibility of retrospective evaluation of the effectiveness of their operation, brought optimization and a significant reduction in costs.
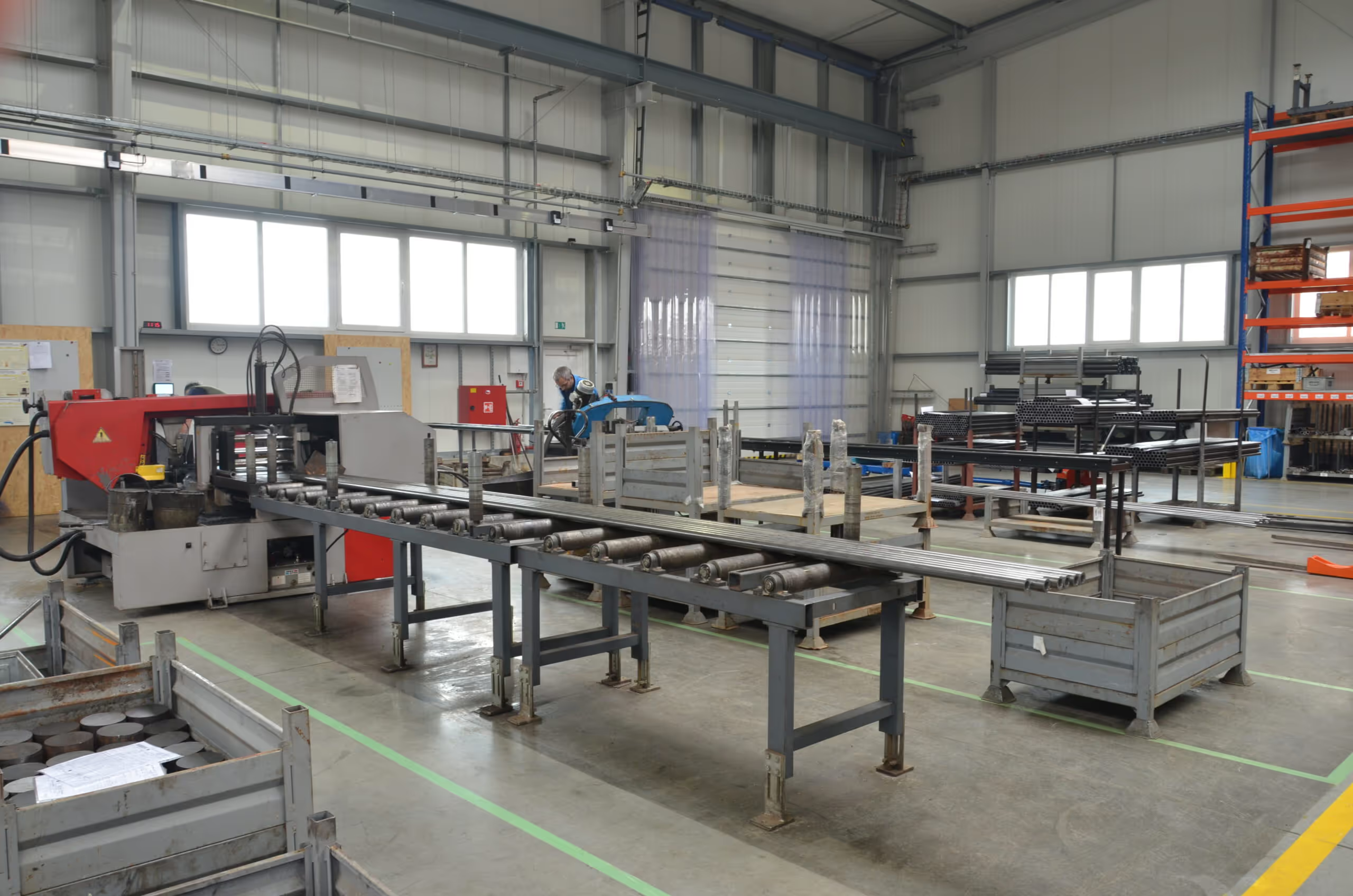
Use of the most cost-effective resources
The system optimizes the concurrence of heating and air handling and ensures the use of the cheapest source available at a given time for a given need. For example, waste heat from production ensures thermal comfort in administrative premises and heating of all DHW.
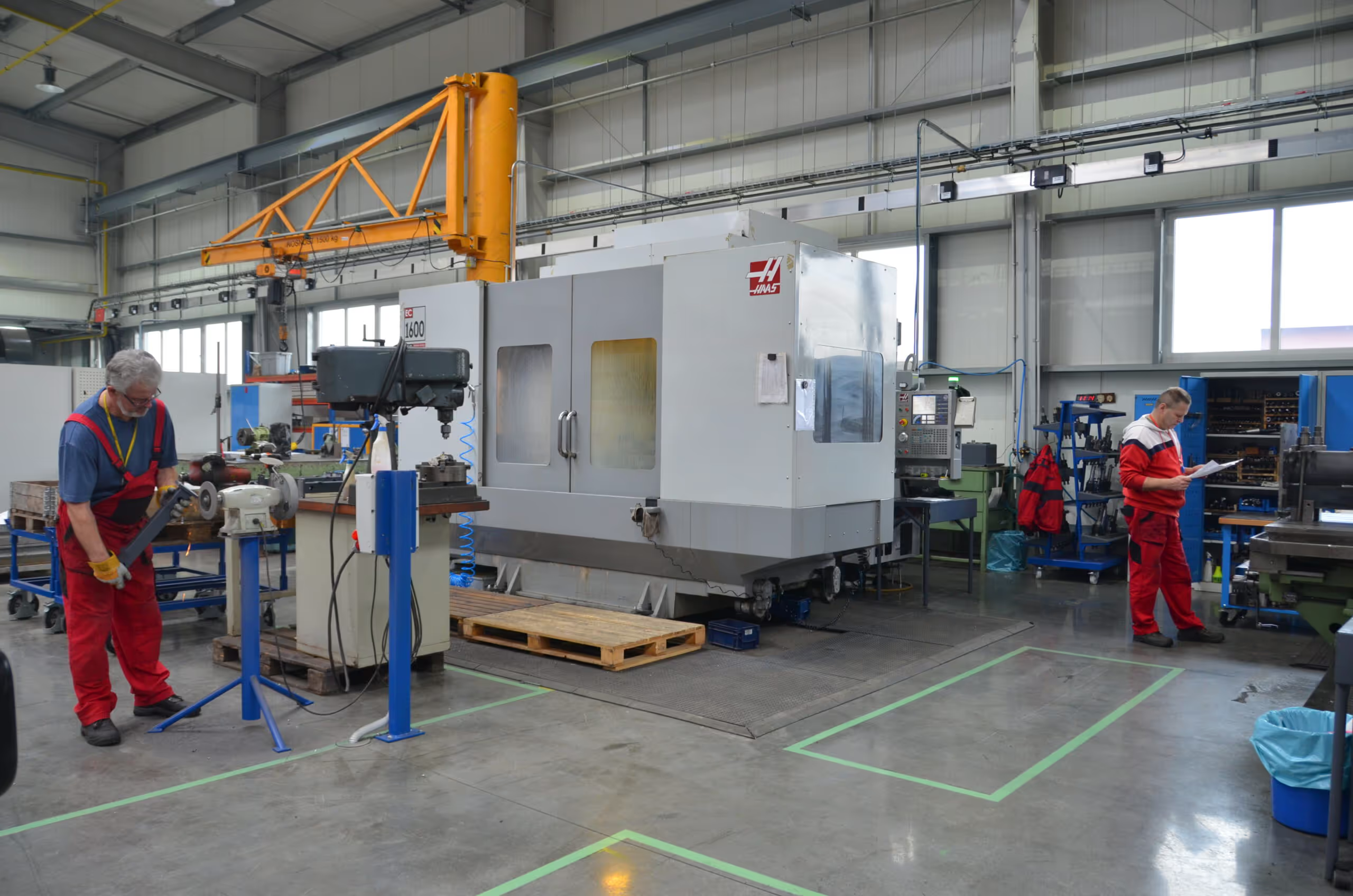
One control unit replaced dozens of others
The FLOWBOX main control unit replaced the heating, lighting, ventilation and air handling control sub-units, thus saving costs for their acquisition or replacement.

Automatic lighting control saves 40 percent
Automatic regulation of the lighting level of the production premises resulted in a 40 percent cost savings.
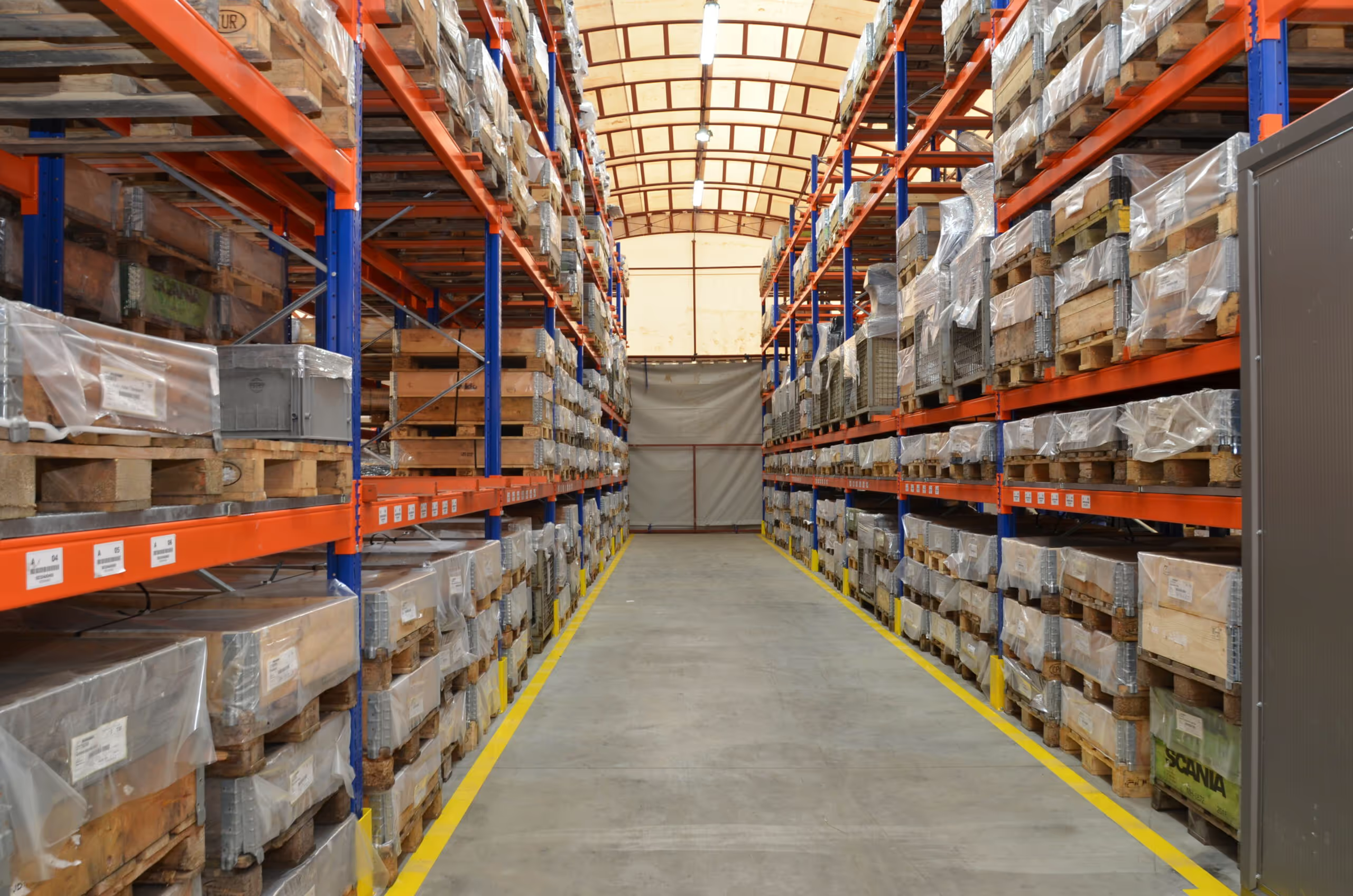
Alarms minimize the risk of accidents
Alarms and links have been created over the individual devices and sub-systems using logical functions that further save time for managers and minimize the risk of failures and accidents in operation.
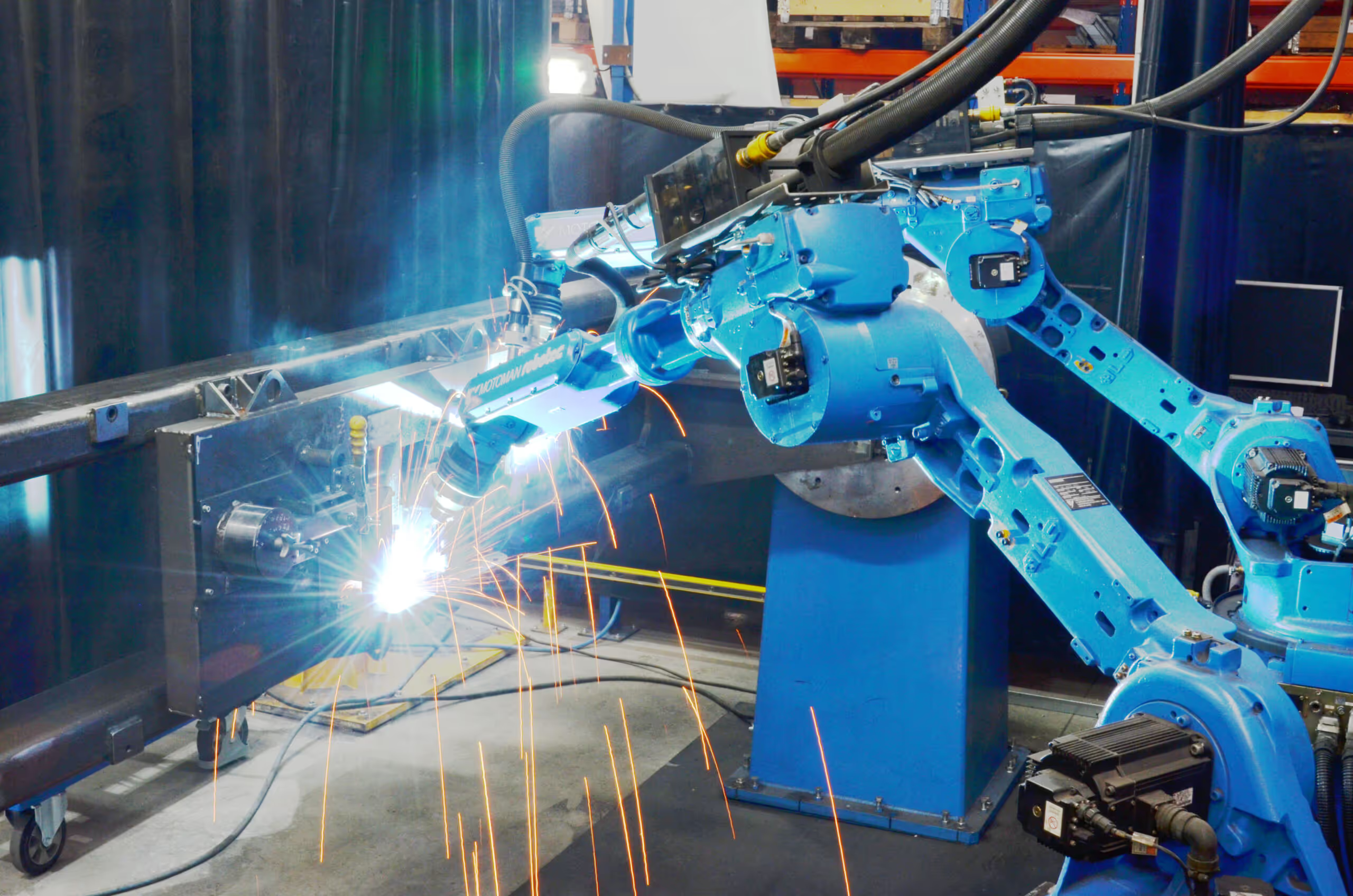
Effective energy management brought 37 percent of an annual savings
FLOWBOX revealed inefficiencies in the production process, which was then optimized. By monitoring all technologies and analyzing the operation in real time, anomalous states are now detected promptly, and production outages are prevented, which minimizes financial losses.
Controlled operation and the correct setting of technologies prolongs their service life and minimizes the cost of repairs. FLOWBOX saves time for staff, operators and even management, who can focus on their core business.
Solution architecture
The heart of the delivery is a Linux server with the FLOWBOX Factory Manager MAN5000 digitalization product package. In the individual halls, secondary decentralized FLOWBOX Alliance Gateways (FAG) FBX5500 with appropriate controllers (PLC modules) and communication gateways with individual technologies and sensor elements were installed.
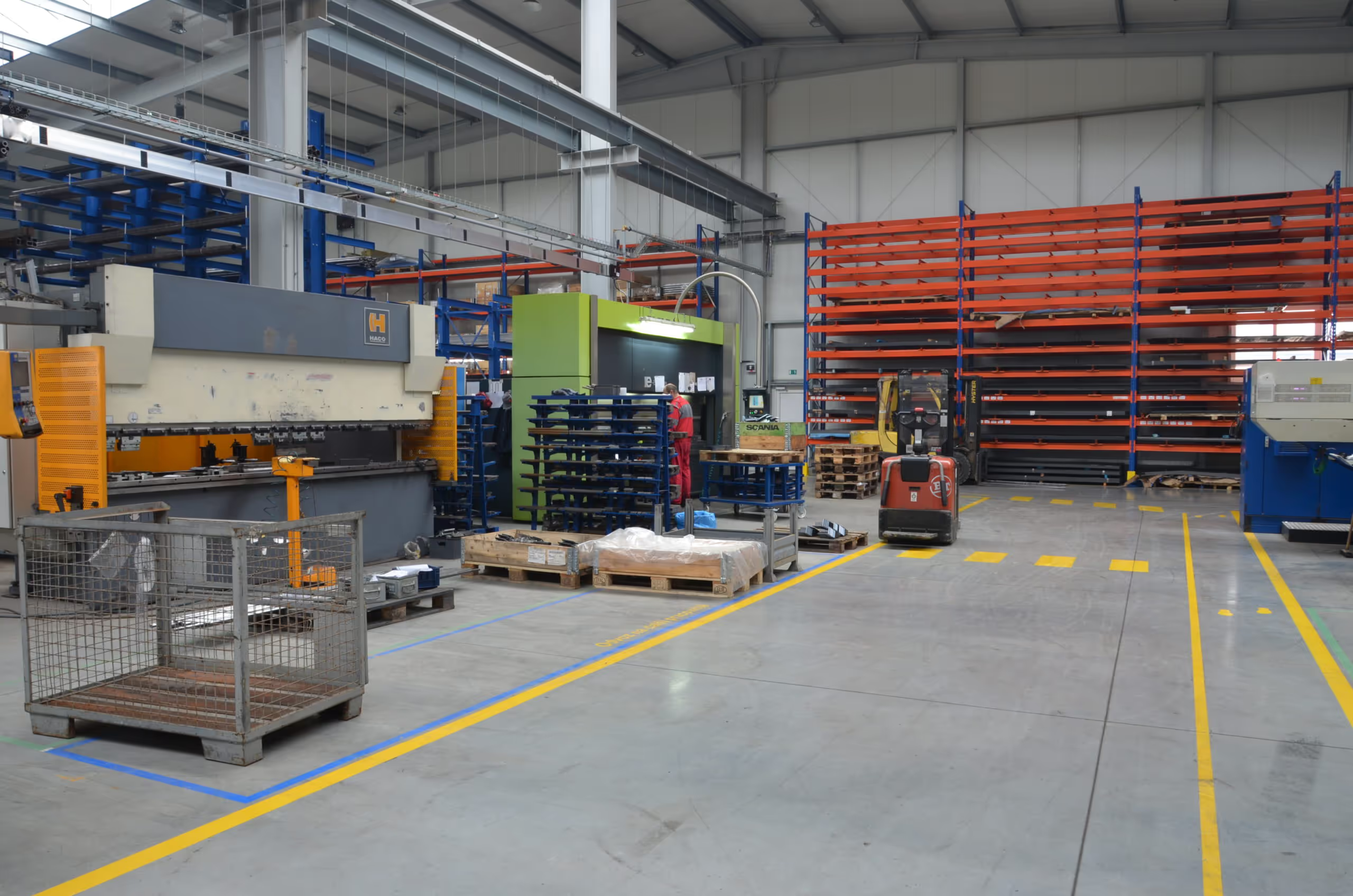
Connection by copper and optical infrastructure
The connection between the FAG and the central server FBX6000 was provided by a backbone dedicated TCP / IP infrastructure (metallic and optical infrastructure).
Communication with individual technologies and sensor elements for supervision, monitoring and their control was ensured by means of bus systems and communication protocols, e.g., TCP/IP, MODBUS RTU/TCP, M-BUS, DALI or 1wire.
Communication with vibration sensor elements installed on individual production technologies was ensured by FBX3400 gateways of a dedicated wireless IoT network LoRaWAN, where one base station covers the entire production space in all halls.
FLOWBOX digitalization solution substantially improved business operations and reduced usage of available resources. It boosted productivity while reduced CO2 footprint.